Enameled Cast Iron Cookware Manufacturing Process
The enamel cast iron cookware is manufactured by a sand casting process. Sand casting is a production process in which shapes are created by pouring molten iron into molds. When the liquid iron cooled, the product is un-molded and removing the sand from the casting, then polishing and spraying the enamel on the raw cast iron and finally baked in the oven. That is Enameled Cast Iron Cookware Manufacturing Process.
1.Foundry
More than 90% of the orders in our company are machine-made.The machine casting blank has the following advantages: 1.strong tightness; 2.good molding,not deformed easily; 3.more suitable for enamel coating;
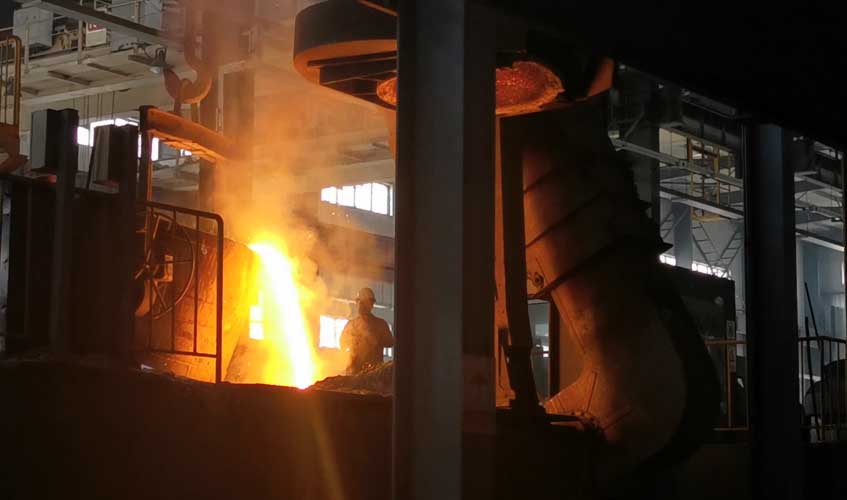
2.Polishing & Blasting
Grinding is for the purpose of polishing the uneven surfaces, flying edges, burr, etc., so that the casting surface is flat. And our examination to the polishing is one by one. Blasting is for the purpose of cleaning the impurities adhered on the surface of the casting,making the castings' surfaces smooth, and be suitable for the technicians to burn.General large castings such as the pot body uses crane, the small castings such as the cover and pan use the blasting method. The inspection of blasting is also carried out one by one.
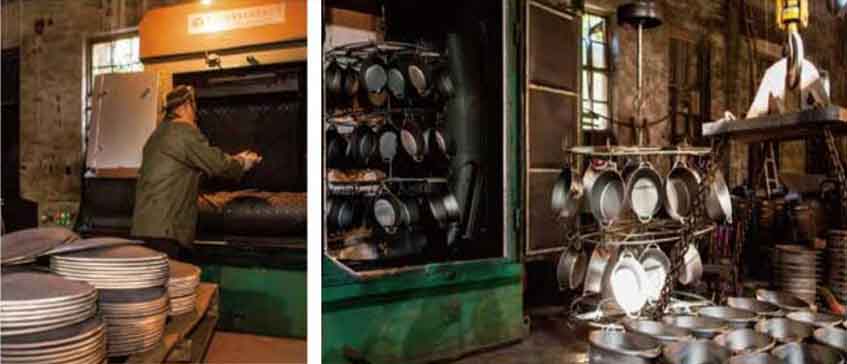
Enamel Frits
Our enamel frit is a independently developed and produced. The recipe time of the colleagues who are engaged in the glaze formulation is over eight years, and they have the background of studying in Canada. Our company is the supplier of China's largest small home appliance group, Midea. The glaze developed by our company is in full compliance with food safety requirements.
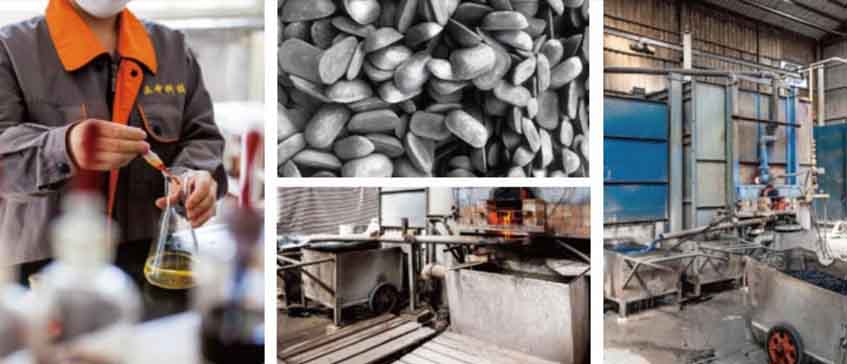
Spray and Enameling
There are three times for the spraying of full-color products in our company:one time bottom glaze, and two times surface glaze. There are strict requirements for the thickness of the inside and outside films of the enamel coating. The matte glaze at the socket is the special glaze. The bottom glaze firing temperature is generally controlled at 770~ 790 centigrade, whereas the surface glaze firing temperature is generally controlled at 740~ 765 centigrade.
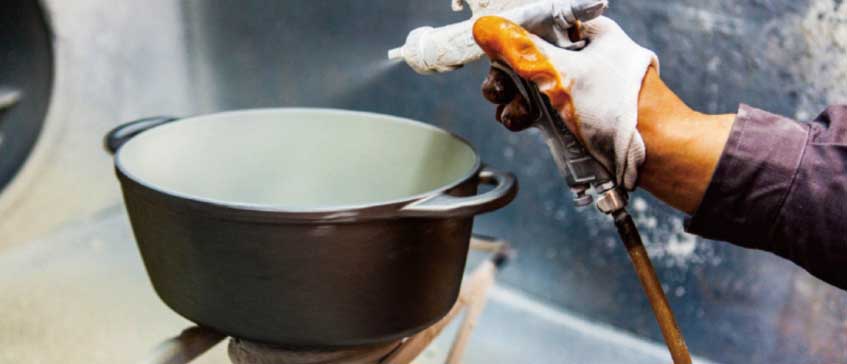
Inspection
The thermal shock test of the induction cooker: heat the induction cooker to 180 centigrade, and carry out a loop every 20 centigrade, the total number of circulations is five, check whether the product has the grain, crack porcelain, and chipping.
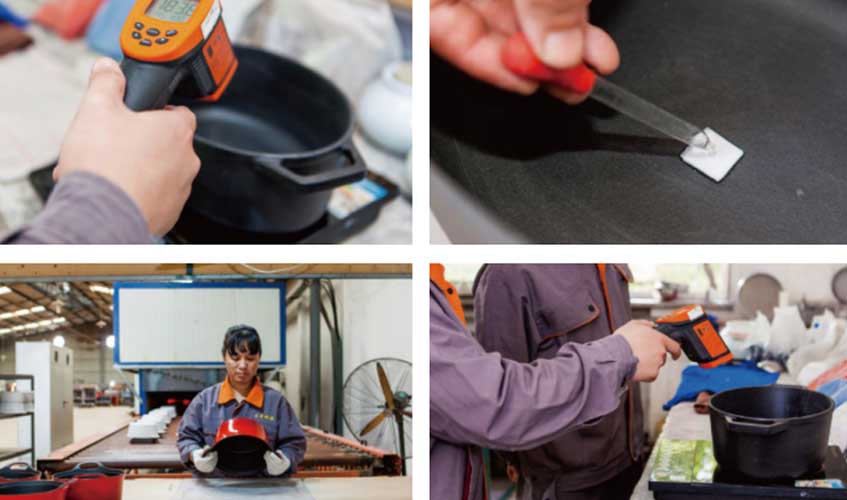
The hitting of steel balls: there is no damage on the enamel surface hit by a 220g steel ball at 1 meter high.
The acid test: the 10% citric acid patch is affixed to any part of the internal enamel surface,and it is covered with a clean surface dish, and remove the patch after 15 minutes, rinse and dry the tested surface by a piece of dry cloth, it is qualified when it is with no corrosion.